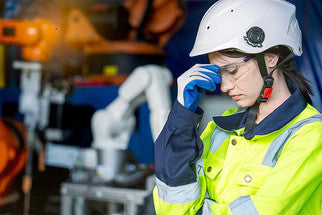
Downtime
When it comes to manufacturing, downtime can be a costly problem. Downtime refers to any time when a factory is not operational, whether it be due to equipment failure, power outages, or other unforeseen circumstances. The cost of downtime can vary widely depending on the size of the factory and the extent of the downtime, but in general, it can have a significant impact on the bottom line. In this blog post, we'll explore the various costs associated with downtime at factories and how they can be minimized. Lost production One of the most obvious costs of downtime is lost production. When a factory is not operating, it is not producing goods, which means that there is a direct impact on revenue. Even a short period of downtime can result in a significant loss of output, which can be difficult to make up for later. Labor costs Even if the factory is not producing goods during downtime, there are still labor costs associated with keeping the factory operational. Employees need to be paid, regardless of whether they are working or not. In some cases, additional labor costs may be incurred to repair or replace equipment that has failed. Equipment repairs and replacement When equipment fails, it often needs to be repaired or replaced. The cost of repairs can vary widely depending on the nature of the problem and the extent of the damage. In some cases, it may be more cost-effective to replace the equipment entirely, which can be a significant expense. Missed deadlines If a factory is not able to produce goods on time due to downtime, it can result in missed deadlines. This can have a ripple effect throughout the supply chain, leading to delays in shipping, missed customer orders, and a loss of goodwill with customers. Increased maintenance costs When equipment is not operating at peak efficiency, it can lead to increased maintenance costs. This can be due to the need for more frequent repairs, increased wear and tear on the equipment, and additional labor costs associated with maintenance and repair. Damage to reputation If a factory experiences frequent downtime, it can damage its reputation. Customers may begin to question the reliability of the factory, which can lead to a loss of business over time. This can be particularly damaging in industries where reliability is critical, such as aerospace or defense. So, what can be done to minimize the cost of downtime at factories? Here are a few suggestions: Implement preventative maintenance programs By implementing preventative maintenance programs, factories can identify potential problems before they become major issues. This can help to reduce the likelihood of equipment failure and minimize downtime. Invest in backup equipment Having backup equipment on hand can help to minimize downtime in the event of equipment failure. This can include backup generators, spare parts, and redundant systems. Train employees on maintenance and repair By providing training to employees on equipment maintenance and repair, factories can reduce the need for outside contractors and minimize the time required to repair equipment. Monitor and analyze downtime By monitoring and analyzing downtime, factories can identify trends and potential problem areas. This can help to inform preventative maintenance programs and other initiatives aimed at reducing downtime. In conclusion, the cost of downtime at factories can be significant. However, by implementing preventative maintenance programs, investing in backup equipment, and providing training to employees, factories can minimize the impact of downtime and ensure that they remain competitive in their respective industries.